...And how does it differ from data mining, process mapping, and business process management?
When people hear the words data mining, they nowadays have an idea of what it means. We often define data mining as a process of analyzing data from several perspectives and summarizing it into useful information. With support from this information, we can then make decisions that affect the success of a company.
However, even if data mining is familiar to people, process mining still seems to be a new topic for many. Very often, I encounter questions like, “What is process mining? How does it differ from traditional business process management"?
In this blog, I compare process mining to data mining, business process management, and process mapping. For more details on how process mining works, why companies do process mining, and the various use cases and benefits for process mining, head over to the ultimate guide to process mining (web page).
Editor's note: This post was originally published in July 2017, and has been updated for accuracy and comprehensiveness in March 2022.
Process Mining vs. Data Mining
On a general level, we aim to do the same with process mining as with data mining. The goal is to analyze data from different perspectives and summarize it into useful information for making businesses run more efficiently.
Combining Business Process Management with Data Mining
However, with process mining, the context of the analysis is the business processes of an organization. In other words, process mining is a combination of business process management and data mining.
Process mining takes the data that exists in the information systems of a company and uses that to visualize the real-life execution of the company’s processes.
Almost all IT systems (such as SAP, Oracle, Dynamics, etc.) store data in databases and create event logs when employees or software robots interact with the system. The event logs are required for process mining analysis (together with time stamps and IDs), and this is what sets process mining apart from other types of data analysis.
Process Mining vs. Business Process Management (BPM)
Process visualization
The traditional methods of workshops, interviews, and manual documentation require a lot of effort. But how else can you update the process documentation and make sure it actually describes the way things are really done?
Process mining software saves you a lot of time and effort. Just take the data, and visualizations of your processes are already on their way. The best part: they are based on facts and are completely objective.
Process mining tools visualize what kind of process flows take place in your organization and how different teams or units are performing.
This empowers process professionals who are responsible for optimizing and improving operational performance with the means to spot inefficient processes or steps within the process and find the best practices in use.
Process improvement and monitoring
Have you looked at processes from an operations-driven or data-driven point of view? Business process improvement as a domain has been around for eons (well, for decades at least), but many companies are still doing it with traditional and subjective methods – workshops, interviews, manual documentation.
If you work in one of these companies, you are overlooking the abundance of data in your own company’s IT systems and how you can use this data to conduct process mining to give a completely new angle to the improvement needs and actions of your organization.
To understand the differences and what to change, you need to be able to compare performance even on a very detailed level to dig out the real root causes. Process mining shows you a list of targets: where to make changes, where the biggest need for improvement is, and most importantly, where the quickest and most significant benefits are to be achieved.
Once you identify the improvement needs and actions needed for your organization based on the results, process mining also gives you the means to easily follow up on the impact of changes in business processes. Not only does process mining software like QPR ProcessAnalyzer visualize the actual process flows, but it also offers a variety of analyses for organizations to understand their processes and monitor how improvement actions are changing them. With the help of the process mining software, you can easily identify where to target your improvement and development activities when new actions are required.
Process efficiency
How much more efficient and in which areas? What are the cost savings? Do you know which units in your organization are doing best and why that is?
Companies need to have all possible information and support at hand to target decisions correctly. Regular KPIs will get you started, but to get down to individual process-related facts, you need to do more. These are facts and numbers that you would not get access to with traditional process mapping.
Automation analysis
Similar to process mining-based efficiency analyses, you will not get accurate answers to questions regarding the success and challenges of automation unless you use process mining software.
Process mining provides instant answers to questions such as:
- Which processes are the most suitable for automation?
- What are the most common process exceptions?
- How does the automation rate of a specific process vary across different countries?
Easily find out how any changes affect the cost savings and efficiency of your processes, for example: view the impact of automation with the click of a button (read: 7 ways in which process mining adds value to intelligent automation).
Process exceptions and variations
If you recognized the need to increase process efficiency, you probably also acknowledge the importance of reducing process deviations.
You might be experiencing trouble with lead times and automation degrees, for example. Customers may not be getting what they requested when they requested it, RPA bots are not performing as they should, and you aren’t really sure why that is the case when individual KPIs show acceptable levels.
You might think some process steps are completely automated, but the company hasn’t really achieved the benefits expected through automation. Undiscovered variations play a huge role in delivering automation that works, as in order to work, RPA bots need to be taught how to handle the exceptions. If you’re not aware of your process exceptions, how could you teach RPA about them?
Process mining automatically uncovers all variations and shows, among other things, the most common or the most inefficient process flows and steps.
Why Process Mining?
Why not just stick to traditional BPM? To answer to the ever-growing pace of business transformation, you need to be able to react quickly and not build analyses that are outdated already before they are completed.
The accumulation of data is making sure that your process analyses cannot be based on gut feelings: you need fact-based figures and evidence to back up your claims.
Saving time and releasing working capitals
Traditionally, managing and optimizing processes has been a very labor-intensive area that requires a lot of time from experts in the organizations. The growing demand for efficiency and being able to clearly showcase results is also hitting BPM professionals. Very often, I’ve heard them state that when their situation analysis is ready, the data which they used to back their assumptions with has already changed, rendering the analysis all but useless.
"Very often, I’ve heard BPM professionals state that when their situation analysis is ready, the data which they used to back their assumptions with has already changed, rendering the analysis all but useless."
When improving processes, the most time-consuming part is often collecting data. With process mining, you get a head start by automating the data collection part. The basis for understanding the operational situation in an organization is to understand what is actually happening, not what is assumed to be happening. This is what you find out using process mining.
Locating process bottlenecks
Process bottlenecks are hard to uncover by hosting process mapping workshops. People have a gut feeling of what could be wrong or inefficient, but they lack fact-based proof.
They need the data to back their assumptions and ensure everyone is on the same page. This is where process mining comes to the rescue.
Replacing opinions with facts
One of the main goals in process mining is to be able to see the big picture of a company’s business processes and still be able to drill down to the root causes of deviations, bottlenecks, or other inefficiencies.
With process mining, we don’t have to settle for averages - we dig out the reasons behind unwanted behavior. To bring this closer to organizations and to see what process mining means for different industries, I’ll give a couple of short examples.
Example: benefits of process mining for the Accounts Payable process
What are Typical Use Cases for Process Mining?
Process mining is beneficial for many situations, especially in large organizations. I can think of a few areas where the process mining methodology has been applied actively, although other areas also can gain immediate benefits from using the same process mining models. You can read more about the most common process mining use cases:
Intelligent Automation: The only way for you to create truly resilient and efficient end-to-end processes.
Procurement: Gain vital insights into your end-to-end procurement process
Process Intelligence: Gain insights into processes, report process KPIs, and monitor process compliance continuously
Digital Transformation: create the best version of your company – based on facts, not guesses.
Auditing: Get an x-ray of your processes
Process Improvement: Achieve process excellence with data-driven process improvement
Order Management: Offer your customers the seamless experience they expect
Service Management: Improve customer experience by making sure SLAs are never broken
IT & ERP Development: Reduce the complexity of IT and ERP migrations, implementations, and deployments
Applying Process Mining to Specific Processes
Typically, people have some idea how the process is running - or how it is designed to run - but the reality revealed with data can prove to be quite different.
Common findings are changes in order-to-cash and purchase-to-pay processes: a single order is delivered several times, or an invoice is sent more than once or left completely uninvoiced. For various reasons, the cases go through several changes that affect the efficiency of the end-to-end process.
In the order-to-cash process, end-to-end lead times or lead times between process steps deserve some scrutiny - check, for example, the lead time from delivery to invoice creation.
In the purchase-to-pay process, the challenges can start already at the beginning of the process, when a PO is created without a purchase requisition or a frame agreement.
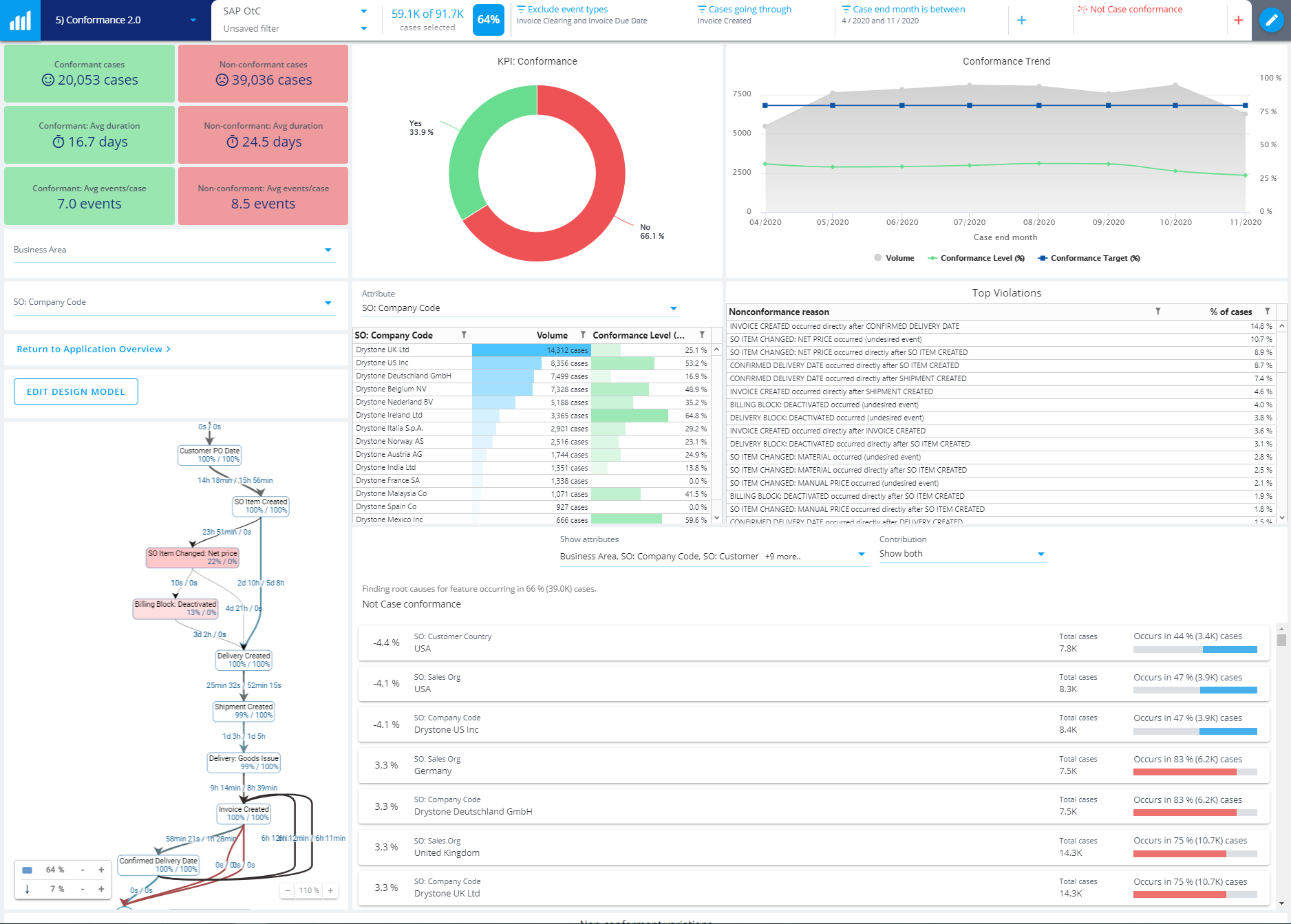
Process mining shows you out-of-the-box how many nonconformant cases you have in your order-to-cash process and root causes for the nonconformance.
Process Mining helps in reaching better on-time delivery and a wider geographical reach. It also helps to cut down logistics and warehousing costs.
Process Mining is used to increase the visibility and transparency of service management processes. It identifies exceptional and unwanted process steps and validates if the escalation rules are effective. Typical incident management KPIs are generated, such as SLA breach rate, Average Time to Resolution, and first call resolution rate.
Applying Process Mining to Specific Industries
Telecommunication
Telecommunication is a highly competitive sector globally. The ability to improve operational processes is key to success and profitability. Process Mining helps telecom companies in creating visibility to geographically disperse operations, identifying bottlenecks and ensuring that customers receive products and services on time.
Manufacturing
In the manufacturing industry, timely and accurate delivery to a customer is the ultimate goal. If a company has several factories in different regions, there usually are differences between the reliability of deliveries. It’s quite easy to see that they exist, but harder to understand exactly where or why they happen. Also, very often, people with the loudest voice gets the most attention regardless of whether their problems are the biggest. With process mining, we can compare the performance of different regions down to individual process steps, including duration, cost, the person performing the step, and many more. All event data available in the systems is suitable for use in process mining and this way, you'll bring the facts to the table without debates.
- Case Studies: Metsä Board, Terumo, Patria Land System, Ruukki, Vaisala. Kemira
- Example: Metsä Board succeeded to increase order lines and volume by 60% without changes in their supply chain headcount as well as increase the number of conformant order lines from 40% to 80% - by focusing process improvement activities to the right areas and improving their geographical reach.
Banking and Financial Services
In the financial sector, it is crucial to follow the rules and regulations and to be able to prove you have done so. By using the event data from the systems, we can visualize even individual cases as a process flow. We can also show how often deviations and variations occur and what has been the reason causing this non-conformance. With process mining, we can both prove our actions but also pinpoint the improvement needs in the business processes.
Management Consulting
Consulting companies play a major role in the development of organizations. Large, medium and small-size consulting companies are using process mining to achieve data-driven improvement which is based on facts instead of assumptions.
- Case Studies: Implement Consulting, EY
- Example: EY UK got a holistic view of all business processes with full coverage of all transactions and root causes of inefficiencies, allowing them to predict errors and prioritize actions based on risk
Retail
The success of retail companies comes from efficient business operations. Logistics, warehousing, forecasting, order management, supplier management form the bases for the excellent end customer experience over the whole end customer life cycle. Process Mining gives visibility to all these interlinked processes providing an understanding of bottlenecks and failing interfaces. Data-driven fact-based Process Mining findings focus the development effort into those areas that matter most and give highest business results.
- Case Studies: Stark
- Example: Stark managed to dig deep into their IT systems and processes in order to streamline and digitize their business processes.
Utilities
Utility companies have a high demand for robust and reliable services for their end customers. Process Mining provides visibility to complete end-to-end processes identifying process bottlenecks and root causes.
- Case Studies: Fennovoima, L&T
- Example: Lassila & Tikanoja used process mining to support their ERP implementation: they gained visibility into data and were able to develop internal capabilities from a process and data driven perspective.
Services
The business logic of service companies is to achieve higher operational excellence (ie. lower costs) than their customers for the particular processes they outsource. Process mining is an important tool for improving the efficiency of a service company by ensuring harmonized operations, finding root causes for process issues and inefficiencies:
- Caverion, Barona
- Example: Caverion reduced the average time for delivery to invoicing by 50%, harmonized processes across the many different countries in which it
operates, and continuously monitors the process to ensure operations remain on track.
Summary: Visualize Processes, Make Findings and Discover Root Causes
In process mining, we use the event data in the company's IT systems (such as ERP, CRM and BPM) to bring insights into the company’s business operations. The insights are provided by automatically visualizing data with process flowcharts and creating analyses that give information on needed improvements and deepen the understanding of what is going on in the business processes. We can show both the big picture as well as the detailed ground-floor view on process execution.
Get started with QPR's process mining software, QPR ProcessAnalyzer.
To learn more about how process mining can be applied in your organization, send us a line, or request a demo. Our experts and I are happy to chat about process mining with you.