In over 30 years of working in business process management (BPM), we have identified the two most common causes of operational inefficiency in large organizations: lack of attention to the "as-is" processes, and lack of means fully to understand them.
This is where process mining steps in. Making sense of the data in your own organization's information systems, process mining software (such as QPR ProcessAnalyzer) offer you a complete, fact-based picture of how your processes perform in reality, identify the bottlenecks, and suggest the actions you should take to fix process problems before they happen.
This blog post will discuss four related topics within BPM: Deming cycle (PDCA), BPM lifecycle, process mining stakeholders, and process excellence KPIs, and how process mining is an excellent tool to support these.
Writer's notes: This blog post was originally published in April 2020, and has been updated in 2022 for accuracy and comprehensiveness.
See the on-demand webinar on this topic and download the presentation slides here.
1. Implement change through the Deming cycle - PDCA
Deming cycle: PDCA is one of my favorite methods for implementing change in any organization. PDCA stands for Plan - Do - Check - Act.
Plan:
In order to improve your business, you first need to analyze your business operations and identify problems that are limiting your performance. All organizations in the world have some challenges either within their operations or caused by their environment. From an internal perspective, one of the most prominent challenges organizations now have to face is digitalization - using digital platforms to make their processes more efficient. All organizations must respond quickly to minimize risks and keep our businesses up and running in the current pandemic crisis.
After successfully pinpointing your organization's issues, you should identify their root causes - what causes these problems. Based on these analyses, you then plan the improvement. This is where process mining software proves to be a powerful tool, as it can quickly discover your as-is processes, their inefficiencies, and root causes based on your data. After implementing process mining, you'll promptly get a complete X-ray of the processes based on the systems that you already have in use. You'll gain the power to make meaningful, necessary decisions based on this fact-based data.
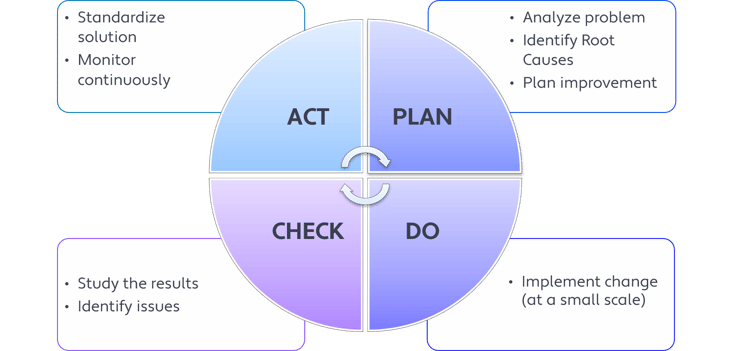
Do:
This part happens outside of process mining. After process mining gives you an in-depth understanding of your processes, problems, and root causes, you'll have a good idea of what to change. The operational development change outcome will then be visible in your transactional system data, such as the ERP, CRM, and Financial systems.
Check:
Now you study the results that your changes bring about and see what is working and what is not. Process mining can pick up these changes in the end-to-end processes and continue monitoring them for you, in contrast to traditional analytics, which is hard-coded in and won't follow new changes in your operations. Process mining helps you verify if the changes are working as intended and if any value is added to your process. This step acts as a bridge between the Do and the Act parts.
Act:
If the changes you made in the Do step work successfully, you will then standardize the solution for your business. It's essential to make sure the solution is implemented, standardized, taken into use, and that it will continue to stay in service. In other words, you should continuously monitor your processes to react timely to future problems. Process mining is used to monitor the whole end-to-end process, ensuring the process improvement works as intended and identifying the new most essential problems limiting performance.
#Tip: A good rule of thumb is implementing small-scale changes in the Do-step, then standardizing or scaling it up in the Act-step.
#Tip: From the process management point of view, process mining is most powerfully used in the Plan, Check, and Act -steps.
#Tip: Remember to give process mining analysis results from the Plan-step to the team implementing the change Do-step, such as the RPA/Process Automation team.
2. BPM life cycle with process mining
The second process improvement topic that I'll cover is the BPM lifecycle. This model is very well aligned with the previous PDCA model, but the way you can utilize process mining with these steps is perhaps more tangible.
This cycle starts from the process identification. No matter what business your organization is in, you have a great number of processes - the two most common end-to-end processes being the order-to-cash (OtC) process (when you are selling and delivering your products and services) and the purchase-to-pay (PtP) process (when you are buying something). From the functional perspective, your organization also has many internal processes in HR, finance, logistics, warehousing, etc. You need a holistic view of all of your operations to identify which processes are critical to your business and add real value to your customers.
As process mining works on a case level (we have a unique identifier and accurate log of events related to each case), it can show you what happens in that one case, and then in one million other cases - adding all up for you to comprehensively understand the whole process.
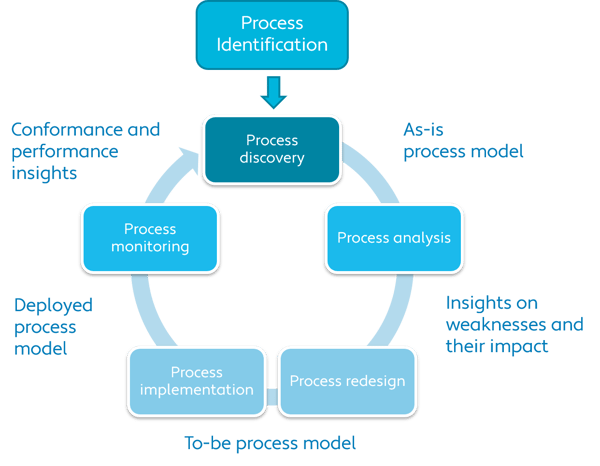
From a process management perspective, you first start with process discovery to understand your as-is process. It's noteworthy that the as-is process model you gain from process mining comes from fact-based data in event logs, which gives superior fact-based transparency to the actual operations for process owners and other stakeholders. These process mining models are much more accurate and detailed than traditional, manually prepared process diagrams.
Once you successfully discover your as-is process, you'll move on to the next step, process analysis, where you look for weaknesses and their impacts on your processes. Process mining provides you with a holistic view of your process where you can quickly identify the bottlenecks of your processes, the rework, as well as the exceptions. An important result from the process analysis is the root cause analysis, which is provided automatically using the process mining tool and is crucial for understanding the operational problems' causes.
In comparison with the Deming cycle, this BPM life cycle is more complex, where your goal is to create a new process model through process redesign and process implementation. Process mining helps you to pinpoint the variations that work well in your organization. Thence, you select a combination of those variations for your new process model. Alternatively, you may implement an entirely new business model and plan the to-be process based on new digital transformation possibilities. Your next step is continuous process monitoring on your newly deployed model. What process mining can do here is give you the conformance and performance insights to see how your new process is performing and how it conforms to the designed process.
The cycle keeps going on like this, increasing your business process maturity and eventually transforming your whole organization.
#Tip: You can apply this BPM life cycle to your whole organization and all processes, but you should start with the most important five to ten key processes.
#Tip: Root cause analysis often shows that the process is working fine in some business areas but fails others. Knowledge sharing between best-performing business areas to problem areas usually helps to eliminate the problems so that there is no need to do a complete redesign for the whole process.
3. Get stakeholders on the same page
Now that you have fact-based, in-depth insights into your processes thanks to process mining, you should think about giving this information to the right people who will take meaningful actions to transform the way your organization works. Based on many projects where QPR helps large organizations worldwide in operational development, I can identify at least six stakeholders that will be heavily involved in and benefited from process mining.
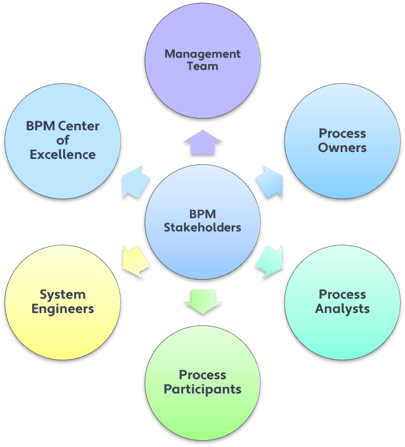
The management team holds the ultimate responsibility for business operations and will get considerable advantages from process mining. The CEO and COO get a fact-based "big picture" of the operations in the whole organization. The CIO is likely to be interested in how the ERP/IT systems and digital processes are working, how the systems support employees to conduct their tasks, and how easy it is for end customers to interact with those systems. The finance directors and the CFO can monitor the waste and rework to reduce costs and increase net profits. Process mining should have at least one C-level sponsor in the management team to provide transparency and fact-based understanding of business operations for decision making.
Process owners are the key people in your organization when it comes to process mining. They manage and monitor the end-to-end process model and the as-is diagrams. In process-oriented organizations, the end-to-end process owners for order-to-cash and purchase-to-pay processes have clear responsibilities and goals related to process performance and resources and decision-making power for implementing changes.
Process analysts are those who work with process owners. They are usually on the business side, which means they analyze how the process works, what the problems are, and how they can improve the situation. In other words, when process owners are responsible for the big picture of the whole process, process analysts are those who utilize the results from process mining in their work.
#Tip: Process owners own the process mining models, and process analysts use these models to improve operations in their business areas.
Process participants are those who work within the actual business operations. Their work produces the event logs used in process mining and process modeling. In practice, the change in fundamental processes results from process participants doing their job differently compared to the past. Change management deals with the potential resistance from process participants when asked to change their old ways of working. Therefore, management needs process mining in change management communication programs to make sure process participants conform to the improved processes, which is more comfortable when the benefits and improvement results are made visible through process mining.
On the IT side, you have system engineers who implement the change into your systems, such as IT, ERP, and CRM systems. For instance, once you've seen results from process mining, sometimes you notice your ERP is not constructed optimally and that it's beneficial to make a change in the system. Other times, you could use robotic process automation (RPA) to conduct some current manual tasks automatically. System engineers are those who set up these changes and make sure your processes can run smoothly. They need input from process mining (handed by process analysts) to see where the problems lie.
Finally, the process mining methodology experts are possibly in a dedicated BPM Center of Excellence in your organization. Methodology experts help other stakeholders in using the process mining methodology and tools. They are in charge of knowledge sharing activities, transferring best practices for process mining usage within the organization. They also communicate results and positive stories achieved with process mining and things to avoid in the projects. In addition to the basic process mining functionalities, the methodology experts are masters of special process mining functions such as advanced root cause analyses, conformance analyses, and AI-powered clustering and predictive analyses.
#Tip: While large organizations have their own BPM Center of Excellence, smaller organizations can have one methodology expert or outsource this function to a company like QPR.
4. Process Excellence
With hands-on experience working with customers from large organizations worldwide, QPR's experts in process excellence indicate the three most important types of KPIs: happy customer, happy flow, and happy automation.
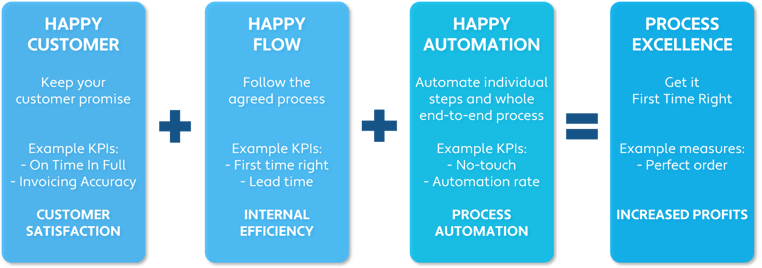
First of all, the happy customer KPIs mean keeping your promises to customers to ensure high customer satisfaction. For example, after customers make purchases with your organization, they should receive the order on time and in full. These KPIs aim to achieve high customer satisfaction.
Second of all, the happy flow KPIs assure that organizations follow the agreed process to accomplish internal efficiency. For example, although you would manage to send the order to your customer on time and in full, you need to use an unusual and expensive way of delivery to do this, your internal efficiency suffers. Examples of the happy flow are first-time-right and lead time KPIs.
Last but not least, the happy automation KPIs help your organization to monitor your process automation progress. You can apply the happy automation KPIs for both individual steps and the whole end-to-end process. (Read more about QPR's solution for Intelligent Automation here.)
You can achieve process excellence for your organization when all these three steps (happy customer, happy flow, and happy automation) are reached for all individual cases. You can use this framework of process excellence to improve all of the processes in your business.
5. QPR ProcessAnalyzer for Process Improvement
QPR ProcessAnalyzer has hundreds of features supporting Process Improvement. This blog will highlight three features with screenshots linked to the corresponding parts of the webinar recording.
Get transparency into your processes using Benchmarking
The ability to discover fact-based, as-is processes is at the core of process mining. QPR ProcessAnalyzer provides you with excellent tools for benchmarking these as-is processes by any dimension meaningful to your organization.
The picture below shows a benchmark of business in the Region: Chicago compared to the other regions. The Flowchart in the left window shows that 22% of cases in Chicago experience Delivery Changed activities compared to only 1% of cases outside Chicago. The table in the right window shows that while 15% of all instances belong to Chicago Region, 42% of those cases where Account Manager is Mary Wilson belongs to Chicago.
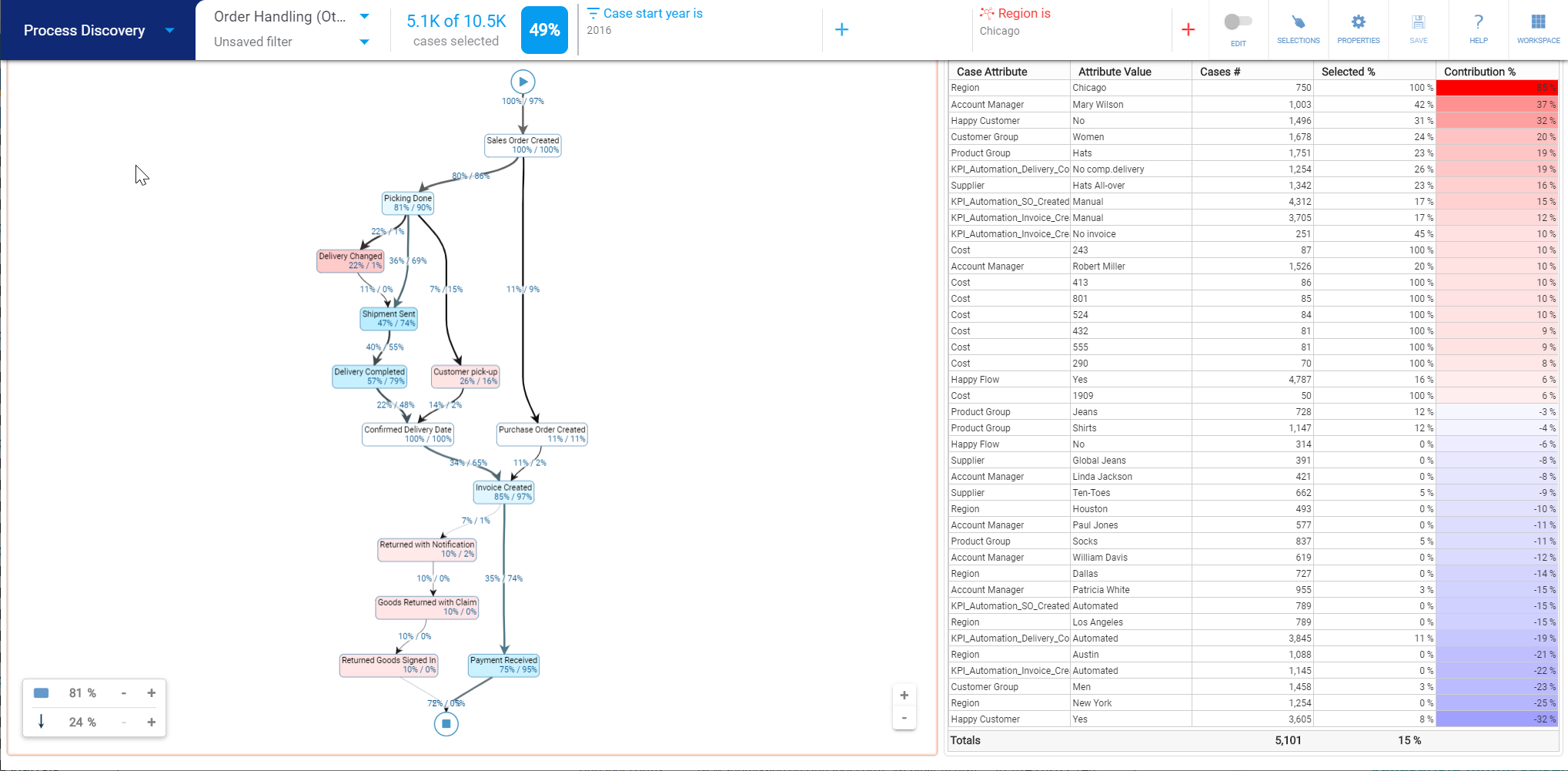
Process Compliance Analysis using Conformance Analysis
Conformance Analysis is a powerful process mining feature that analyses the actual as-is process behavior with the intended design process flowchart. In the picture below, 45.2% of all cases are compatible with the Design Model, and 54.8% are nonconforming. The Conformance Trend shows the monthly conformance level following Top Violations and Top Variations.
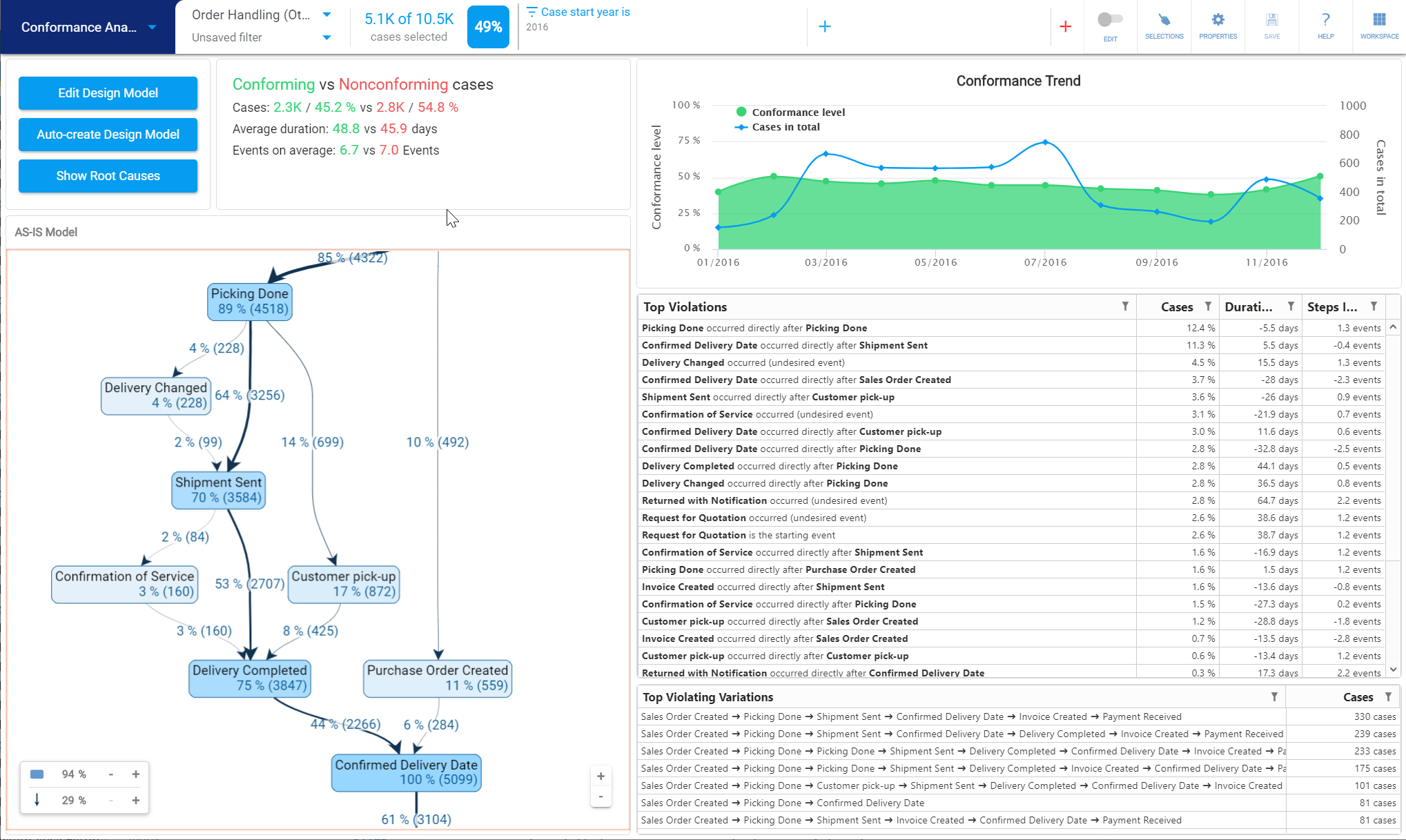
Continuous Monitoring with Dashboards
QPR ProcessAnalyzer contains full Business Intelligence, reporting, and analysis features, which help you communicate process mining results to all process mining stakeholders. You can select KPI charts from ready-made presets and easily customized them by any user. Moreover, detailed custom KPIs are easy to create with the powerful expression language, using the underlying process mining model. You can freely add all KPIs and charts to custom dashboards, like the one below, showing the On-Time Delivery Trend, Invoice Automation Rate, and Sales Order Line Item trend.
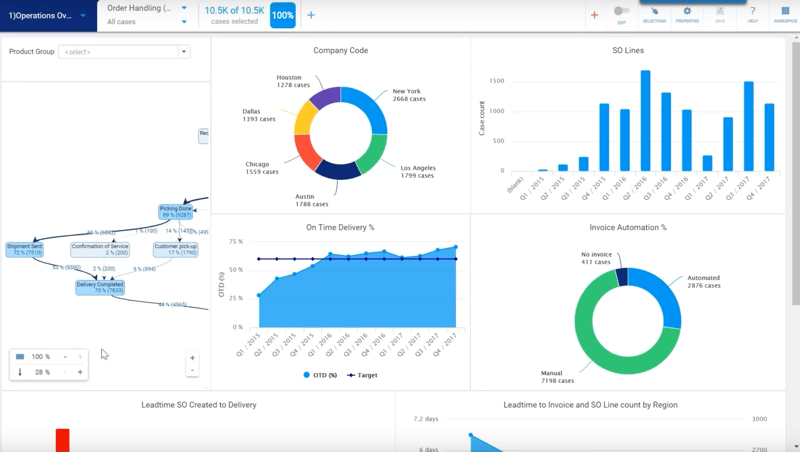
It’s a good time to take a look at Process Mining if your company hasn’t already. The capabilities and usability of Process Mining software are improving rapidly, and the market is quickly becoming mature, although there’s still much work to be done. If you think your company is ready to step it up with the future of as-is process modeling and process efficiency maximization, the fastest way to get things moving is to follow these steps: