Metsä Board eliminates uncertainties with QPR ProcessAnalyzer
Process mining helps to create better customer experiences, a better work environment, and cost savings
By carefully analyzing and identifying bottlenecks in processes, Metsä Board created a better customer experience. But it didn’t stop there. They were also able to improve the work environment for their employees by eliminating uncertainties and unwelcome surprises from faulty processes.
“ProcessAnalyzer essentially helped us to create a better workplace for our employees because we removed uncertainties from our business processes, and thereby from everyone’s work day. Better processes mean more peace of mind at work.”
Matti Ketonen, VP of Supply Chain at MetsäBoard
MEET OUR CUSTOMER
Metsä Board
Metsä Board is a leading European producer of premium fresh fiber paperboards, such as folding boxboards, food service boards, and white kraftliners. They develop innovative packaging solutions which create better consumer experiences with less environmental impact.
Revenue: 1.932 billion
Operating countries: 19
Employees: 2 400
Solution: Process mining with QPR ProcessAnalyzer
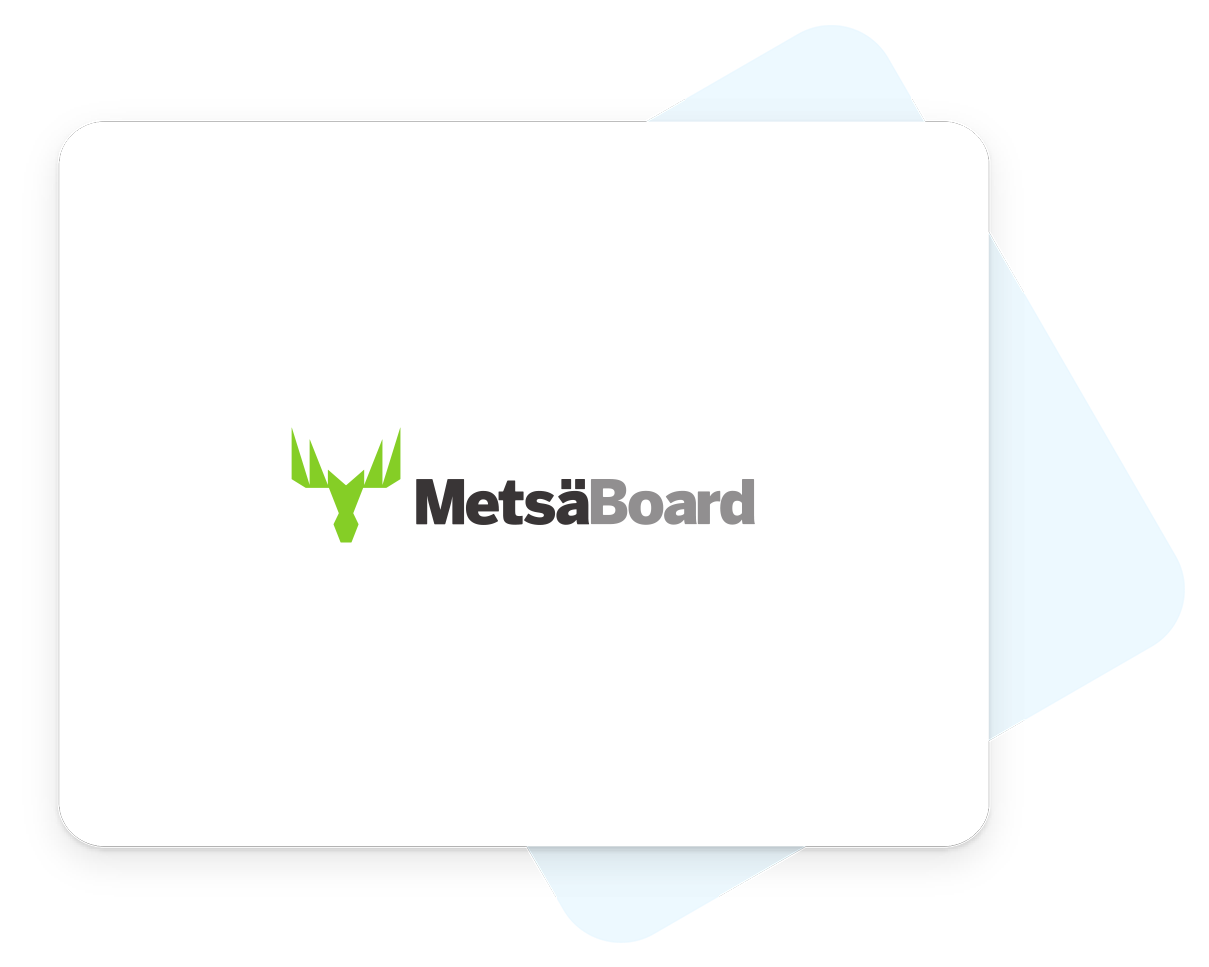
The challenge – outdated systems and lack of unified end-to-end processes
Metsä Board is a leading European producer of premium fresh fiber paperboards, which has transformed its business from producing paper cranes and printing paper to providing packaging materials such as paper boards.
As Metsä Board underwent a big transformation, its core processes were powered by an ERP system that was designed for an entirely different business case.
It was impossible to carry out any process improvements as the ERP did not reflect the latest business scope or structure: it consisted of an obsolete supply chain tool design and was missing integrations to existing functions. Process performance and deviation measurements were missing as well, with business operations reporting a lack of transparency.
For these reasons, Metsä Board started an initiative to improve predictability and harmonize its operating models to provide a better customer experience:
They wanted to transform the way they managed their order-to-cash and forecast-to-availability processes, and needed process insights from SAP data to identify bottlenecks and relevant improvement actions.
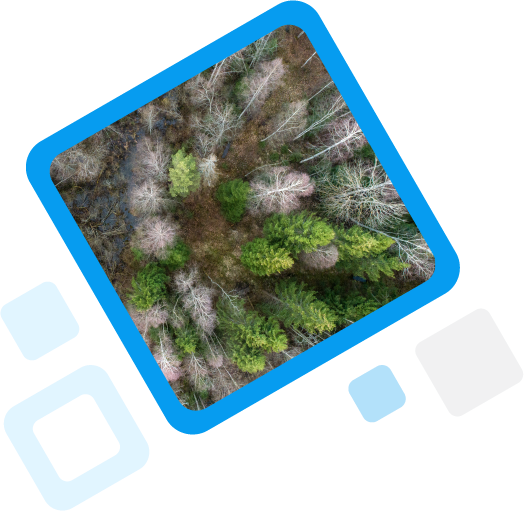
The solution – visualizing processes and finding the right actions
The first step was understanding how the order-to-cash process worked.
Metsä Board used QPR ProcessAnalyzer to map out their end-to-end processes using data that came from SAP. This analysis went beyond existing SAP reports and helped Metsä Board to understand and visualize where the process performance was affected. They found out that changes were made to orders mostly due to ad-hoc requests and as internal adjustments to already made changes.
Metsä Board used the insights from the process visualization to decide on the next steps to take.
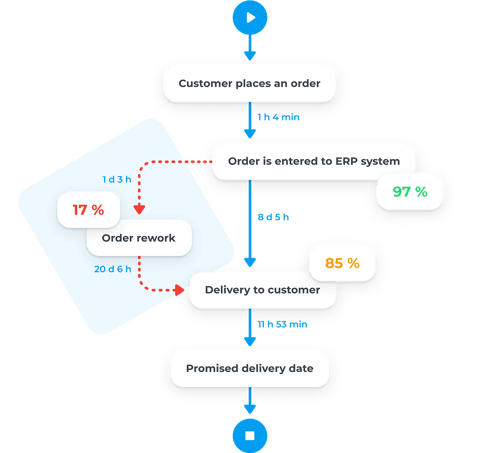
Harmonizing processes through priceless process insights
“The process insight and facts delivered by QPR ProcessAnalyzer were priceless. We were immediately able to focus our process improvement activities on the right things to reach the results our business needed. And not wasting time on trial and error.”
Matti Ketonen, VP of Supply Chain at MetsäBoard
For the following two years, Metsä Board focused internally on harmonizing their supply models and defining the target state of the order-to-cash process, as well as how people should work with these processes to ensure optimal efficiency and less disturbance in everyday operations.
The goal of this development work was to improve customer satisfaction through better delivery accuracy, production efficiency, optimized stock rotation, and reduced number of changes. Besides these customer-centric goals, it was also important to reduce the hassle that inefficient processes had created for Metsä Board’s own employees.
Why QPR ProcessAnalyzer
As your business grows, so does its complexity. We offer an enterprise solution that not just keeps up but expands to better serve your growing needs.
- Flexible, dynamic, and transparent
- Processes billions of complex data rows at an unprecedented speed
- Easy to set up and use
- A modern all-in-one solution that requires no data duplication
- Serves the entire enterprise: no need to upgrade each time you want to analyze another process
- Unique 1-click root cause analysis
- Highly secure and compliant with modern data governance
Results – improved ways of working and no additional software development costs
After analyzing their processes, Metsä Board found that they needed to concentrate on updating their ways of working, rather than using any additional software development resources.
Without ProcessAnalyzer the assumption may have been that the software was outdated and new developments were needed. However, one of the key findings after the review with ProcessAnalyzer was that they didn’t need to make any additional software updates – which are often costly.
The set-up of the existing processes was not broken. The big revelation was, however, that the process had developed a life of its own. In other words, the way the processes were used in the everyday life by Metsä Board’s employees was not consistent. This created a lot of inefficiencies in the process.
Instead of using resources for additional software development or drawing up a completely new process, Metsä Board focused on training their employees on the agreed process guidelines. They didn’t need to make any further investments into SAP development work.
Reviewing their processes with ProcessAnalyzer resulted in these main results for Metsä Board:
✅ Conformant order lines went up from 40% to 80 %.
✅ Order lines and volume increased by 60% – with the same supply chain headcount.
✅ Geographical handicap was successfully mitigated.
✅ Instead of working on SAP development, they developed their ways of working – saving on costs of SAP development work.
✅ Internal change management is driven by facts uncovered through process analyses.
Getting stakeholder buy-in
Reaching optimal process performance requires continuous work and process owners, who regularly monitor key processes with QPR ProcessAnalyzer.
Today, process development activities are based on facts instead of mere hunches. Having real-time data and process visualizations also helps get buy-in for the changes.
Moreover, facts delivered by QPR ProcessAnalyzer have also acted as an effective tool for change management and a means to engage different stakeholders.
“If you are looking after your team and the piece of process you run, what’s better than getting a warning when something goes amiss and then drilling down to the root causes why that is happening.”
Matti Ketonen, VP of Supply Chain at MetsäBoard
“If you are looking after your team and the piece of process you run, what’s better than getting a warning when something goes amiss and then drilling down to the root causes why that is happening.”
Matti Ketonen
VP of Supply Chain at MetsäBoard
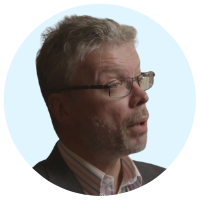
Interview highlights
Want to try it too?
If you have any questions, please talk to the real person in the chat window on your right and you’ll get an immediate answer.
Alternatively, you can fill out this form and we’ll get back to you within the next 24 hours.